Imagine a microchip the size of a grain of salt attached to every single manufactured product in the supply chain. Every can of soda, package of razor blades, pair of jeans…everything. Each microchip contains a unique code. That means, in a carton of sodas, there are 12 cans with 12 microchips with twelve different codes. A pallet of soda cartons might contain hundreds of individual cans with hundreds of unique codes.
Now, imagine that pallet of soda on a truck loaded with dozens of other pallets of merchandise, again, each with its own microchip and code, pulling into the loading dock at your distribution center. As each pallet is unloaded from the truck, a special reader at the doorway reads the thousands of unique codes coming off the truck and automatically enters the items into your inventory. No hand scanning, no unpacking, no verifying counts…simply, unload and warehouse the pallets.
Now, imagine your store with those same readers not only integrated into your receiving dock, but also integrated into your shelving and customer entrances. When a customer removes a carton of sodas from the shelf, the inventory system automatically alerts someone to restock the shelf. As stock is removed from the backroom to replenish the shelf, the inventory system keeps count. When backroom stocks reach specified limits, your distribution center is automatically notified to ship more sodas.
Throughout this whole process, nothing is scanned in the traditional sense. No one is keeping track of quantities of SKUs. Your entire inventory is invisibly, automatically, and, yes, accurately maintained by the millions of tiny microchips communicating the whereabouts of every single item throughout your corporate system.
If that’s not intriguing enough, consider the customer who picked up that carton of sodas from your shelf. Instead of waiting in line and unloading her entire shopping cart at the front end, a reader near the exit automatically reads the entire contents of the shopping cart in an instant, displays the total amount, and the customer can leave with a swipe of her debit card or scan of her fingerprint.
At home, a reader attached to her refrigerator automatically updates her personal grocery inventory on her PC. And every time little Johnny grabs a soda, the grocery list for next week is updated.
Wait…it doesn’t stop there. When those empty soda cans are picked up at the curb by the recycle truck, the microchips still have a job to do. Readers integrated into the recycling center’s sorting equipment will not only automatically sort the various containers into similar materials, but conceivably sort the containers by manufacturer, so that the soda cans are returned to that manufacturer for recycling.
Science Fiction or Reality?
Sounds like science fiction, doesn’t it? But this science is, in fact, currently in research and development at three of the world’s most prestigious universities: the Massachusetts Institute of Technology (MIT), University of Cambridge in England, and University of Adelaide in Australia.
But it’s not just formulas on a chalkboard. Prototypes have been in field testing for almost a year tracking pallets of merchandise from various distribution centers around the U.S. to a Sam’s Club and Wal-Mart store in Tulsa, Oklahoma. A second phase of testing began this summer tracking cases of inventory to test the system’s capacity for handling higher volumes of inventory.
This innovative program is the result of a unique collaboration of academia and leading manufacturers, retailers, and other corporate sponsors. Today’s research is focused strictly on supply chain and store-level inventory management. The consumer-related applications at the checkout counter and in the home described above are not currently part of the research and will likely be dozens of years in the future.
The genesis for this program began in 1998 when two professors at MIT proposed a system-level approach to automatic object identification based on RFID technology. In 1999, the two researchers, Dr. David Brock and Professor Sanjay Sarma, met Procter & Gamble’s Kevin Ashton, who was developing strategies for placing smart chips in everyday items in the retail business. The end result was the formation of the Auto-ID Center within the department of mechanical engineering at MIT in October, 1999. Ashton, on loan from Procter & Gamble, is currently executive director of the center, and Sarma is research director.
The initial funding for the center was provided by the Uniform Code Council, Proctor & Gamble, and The Gillette Company. Today, over 50 companies are involved as sponsors of the center.
Combining Old and New Technologies
Most retailers are somewhat familiar with RFID technology because it is one of the technologies used in electronic article surveillance (EAS) tags. The first application of RFID (radio frequency identification) technology goes back to the 1940s. Large, powered RFID transponders were placed on allied aircraft to identify friendly aircraft using a radar signal.
Subsequent research and advances in technology, including the invention of the microchip, allowed RFID applications to get smaller throughout the 1970s and ‘80s. One of the most significant advances allowed RFID tags to become passive, meaning no battery or source of power is required on the tag. Instead, the tag actually uses power collected from the signal transmitted by the tag reader. Because of the minute power exchange involved in this manner, tags and readers must be within limited physical range to work correctly.
Today, technology allows the miniaturization of RFID microchips to about the size of a grain of sand. This size reduction, combined with sophisticated computer and software applications, is the foundation of the auto identification research.
At the heart of this system is a unique numbering scheme called the electronic product code (EPC). Similar to a barcode, the EPC uses a string of numbers to identify an item’s manufacturer and product category. A third set of digits, not unlike a serial number, is added to the string to give each microchip a unique identification.This unique number is the only information included on the chip.
When a reader sends out its electromagnetic waves, the microchip uses the power from those waves to transmit back the EPC embedded in the chip. The reader becomes a collection point for a software technology developed at the Auto-ID Center called Savant, which is the backbone of the network.
When the Savant system receives the EPC from a reader at the loading dock or store shelf, the information is sent to a company’s local area network or Internet site to a database that associates that EPC with a product. New addressing protocols and software languages have been developed to accommodate this process.
As you can imagine, with the potential for tens of millions of EPCs circulating in the supply chain, managing this tremendous amount of data is perhaps the most challenging part of this new technology.
Moving to this Brave New World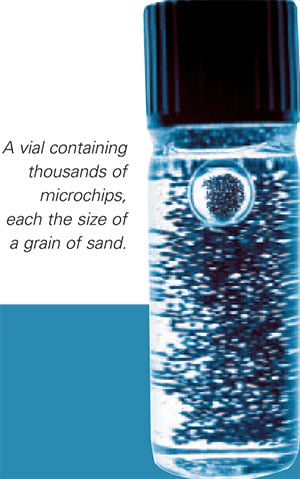
Much work is left to be done before this technology is implemented throughout the supply chain. The field testing that began in October 2001 in Oklahoma is moving the process forward rapidly. Field testing is helping debug the new software languages and protocols developed for this program as well as the necessary hardware. The ultimate goal of the field testing is to prove in a real-world setting the validity of the concept on a small scale before wider implementation.
At the same time, the Auto-ID Center is partnering with sponsoring technology companies to bring down the cost of RFID tags and readers. One of the critical needs to make this system a reality is lowering the cost of the RFID microchip from its current cost of about $1 each to the 5-cent range. Affordable, flexible, and low-cost readers are also in development by other sponsoring companies, with the goal of selling for under $100 each, about one-tenth of their current cost.
The target goal is to have both hardware and software products commercially available by the fourth quarter of 2003.
Once this new system is fully implemented throughout the supply chain, the benefits can be tremendous. Transition costs will be reduced. Lead times for manufacture and delivery will get shorter. Inventory costs will go down, while product availability will go up. At every step of the supply chain, there will be better accountability with better security, safety, and traceability.
From a loss prevention and security perspective, a fully implemented system will certainly help reduce retail shrinkage, internal and external theft, as well as product counterfeiting and diversion.